When producing wire through the wire drawing dies, it is typically not directly drawn but first subjected to surface pretreatment. The degree of refinement in surface pretreatment significantly impacts the service life of the wire drawing dies.
The first step upon receiving the raw materials required for drawing is to inspect them. Non-destructive testing techniques (such as ultrasonic testing) can be used to check for internal or surface defects in the wire, ensuring its quality meets the requirements.
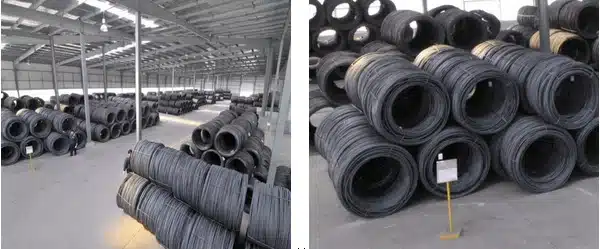
The quality of the raw wire has a significant impact on the entire drawing process. Poor-quality raw materials often lead to issues such as wire breakage, scratches, and damage during the drawing process. Grinding machines must be used to rework wires with surface defects like peeling, pits, and heavy skins before drawing.
For more information about the causes of wire breakage, see our previously edited article “11 Causes Of Copper Wire Breakage.”

If the wire quality is subpar, it is generally recommended that you switch to a higher-quality wire supplier to improve the yield of the finished products after drawing. Alternatively, surface pretreatment of the raw wire can be carried out.
This article briefly introduces several standard wire surface pretreatment methods:
1. Cleaning and Drying
For wires with dirty surfaces or a lot of attached impurities, cleaning is the first step to remove dirt and impurities from the surface. After cleaning, the wire needs to be dried to ensure no residual moisture remains, which could cause quality issues in subsequent drawing processes.
2. Pickling and Chemical Treatment
For wires with a significant amount of scale on the surface, pickling is a necessary step to remove the scale. Other chemical treatment methods, such as alkaline washing and neutralization, might be used to further remove chemical residues or particular impurities from the wire surface.
3. Grinding
If the wire surface has defects like peeling, pits, or heavy skins, grinding machines must be used for reworking. Grinding can remove these surface defects, providing a smoother surface that helps improve the wire’s quality.
4. Heat Treatment
For wires that are too hard or have uneven hardness, heat treatment (such as annealing or tempering) is necessary. Annealing and tempering can reduce the hardness of the wire and make its hardness uniform. Wires with moderate and uniform hardness are more suitable for subsequent drawing processes.
5. Surface Lubrication Treatment
A lubricant layer is usually applied to the wire surface to reduce friction between the wire and the die during drawing and improve drawing efficiency. Standard methods include phosphating and soaping treatments.
Employing the above surface pretreatment methods can significantly improve the wire quality, extend the service life of the wire drawing dies, and enhance the efficiency and yield of the drawing process.