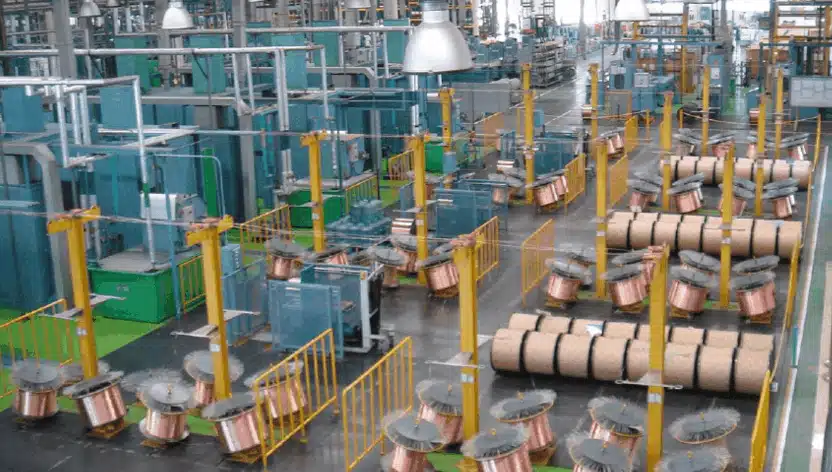
Wire drawing is an important industrial process. Wires are reduced in diameter through a series of wire drawing die combinations, which provide the desired reduction steps.
1、Wire rod stretching
Wire stretching refers to the wire blank in a certain tensile force, through the mold hole plastic deformation, so that the cross-section decreases, the length increases a pressure processing method.

2, the characteristics of stretching
(1) The stretched wire has a more accurate size, surface finish, cross-section shape can be varied.
(2) can stretch large lengths and various diameters of the wire.
(3) mainly cold processing, stretching process, molds, equipment, simple, high production efficiency.
(4) Stretching consumes energy, and the extent of deformation is subject to certain limitations.
3. The principle of stretching
Stretching belongs to the range of pressure processing, stretching process, in addition to producing a very small amount of chips, the volume change is very small, so stretching before and after the volume of the metal is basically equal.

4. Factors affecting the stretching
(1) copper, aluminum rod (line) material. In other conditions are the same, pulling the copper wire than pulling the aluminum line of the tensile force, pulling the aluminum line is easy to break, so pulling the aluminum line should take a larger safety factor.
(2) material tensile strength. Material tensile strength of many factors, such as the chemical composition of the material, calendering process, etc., high tensile strength is a large tensile force.
(3) Deformation degree. The greater the degree of deformation, the longer the length of the deformation section in the mold hole, thus increasing the positive pressure of the mold hole on the line, the friction also increases, the tensile force also increases.
(4) The coefficient of friction between the wire and the mold hole. The greater the coefficient of friction, the greater the tensile force. The coefficient of friction is determined by the wire and mold material finish, the composition and quantity of lubricant.
(5) The size and shape of the working and sizing zones of the wire die hole. The larger the sizing zone, the greater the tensile force.
(6) line die position. Line die placed incorrectly or skewed die base will also increase the tensile force. Also make the wire diameter and surface quality is not up to standard.
(7) External factors. The wire is not straight, the jittering of the wire during the pulling process, and the resistance of the unwinding will increase the tensile force.
The key component in wire drawing is the wire drawing die. For more information about wire drawing dies, see the “About wire drawing dies” page.